Horizontal Stabilizer
If
you follow Vans instructions (usually the best idea), the Horizontal
Stabilizer (HS) is the first item on the Agenda. Personally, I would
build the Vertical Stabilizer first as it is less complex. It seems
a little daunting at first, but the best option is to dig right in.
The HS is, like most of the airframe, a sheet metal skin riveted to
a preformed sheet metal skeleton. The first image below shows the left
side of the HS assembled with temporary rivets ("clecos",
those long things sticking out of the skin). The shiny ribs are part
of the skeleton. the blue stuff is plastic protective coating on the
skin (some has been removed to access assembly holes. It is not rocket
science.
1.
Central Elevator Horn Bearing Assembly
The
instructions ask you to complete the central bracket assembly for the
central elevator horn bearing before proceeding with the actual HS construction.
The second image was my initial result which seemed OK until I bolted
it to the completed stabilizer. The bracket plates with the mounting
holes were slightly misaligned, which meant that the bearing did not
locate exactly perpendicular to the spar - not good. So l drilled out
the assembly, and made a template out of a piece of robust aluminim
angle, with four holes in the exact same positions as the spar mount
holes (see "drilled out" below). I then bolted the loose assembly
to the template with the bearing in place - this ensured that everything
was square (see "Bolted to template" below). With everything
bolted in, I then riveted the assemply together. Previously I had only
used clecoes in the bearing attach holes (as per instructions) to align
the structure but obviously this was not good enough. In future I would
use this technique for similar assemblies to be safe.
The
big lesson learned here was not to be scared to drill out rivets and
reconstruct when things are not optimum. Unfortunately this was an important
lesson for me to learn!

one side of
the HS
|
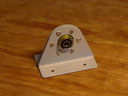
Inital effort
|
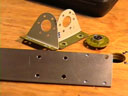
Drilled out
|
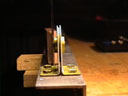
Bolted to
template
|

daylight
|

now its square
|
2.
Horizontal Stabilizer Front Spar
- preparation
This
is where most builders confess to having to study the plans carefully.
The channel section lengths forming most of the spar are actually from
another aircraft kit. You have to modify the inboard section as shown
in the plans below. I used a pen to mark exactly how much metal to remove
and then used a light hacksaw, trimming and finishing with a die-grinder
and Scotchbrite wheel. A Unibit drill provides large stress relief holes
to the central tab,where a 6 degree bend will eventually be provide
sweep in the front spar assembly. The right and left front spars are
held together by two pieces of angle aluminium which need to be trimmed,
drilled and bent to the 6 degree sweep. They are confusingly called
"splice" and "reinforcement" angles. One of them
is the front attachment of the stabilizer to the fuselage! For this
reason it has to be made flat (to abut the fuselage sheet), so the attaching
rivets are flush and they fit into countersunk and dimpled holes as
shown
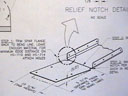
modifications
|
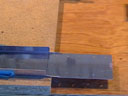
marked up
|
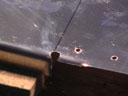
stress relief
|

both sides
|

reinforcement
|
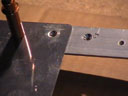
countersunk
- dimpled
|
3.
Front spar to ribs attachment
The
plans show a sectional view of how the inboard ribs and central front
spar assembly go together. It seems confusing, and you have to stare
at the plans for a while to see what's going on. Key is the fact that
you have to trim the ribs as shown to allow just enough space for the
reinforcement angles. Everyone seems to remove too much material here,
and then fret that they have made a big mistake and not left enough
material between the hole and the component edge. I did. But Vans will
tell you that the standard rivet-to-edge limitations do not apply here,
as the components never have shear forces applied because the skins
hold it all together anyway. No worries, mate. Just cleco on the skins
and you are ready to match drill.

confusing
|

5 components
|

together -
side
|

drilling through
|
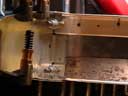
oops - edge
tolerance?
|

together
|
4.
Drilling, deburring, dimpling, preparation and priming
The
skins are clecoed to the skeleton and all holes are drilled out to final
size. Then (as with all components), you disassemble, debur ALL holes,
and dimple as required. I found the Avery vice-grip dimpler did an inferior
job. I only use it in tight spots where there is no alternative. I use
the C-frame or hand squeezer with all holes now. Don't forget to run
the edges of every component along the Scotchbrite wheel to remove manufacturing
artifacts. Use a Scotchbrite pad to remove other imperfections. This
is the most time-consuming bit. I listen to classical music and the
time flies. Once all that is done, wash everything with detergent/Scotchbrite
and rinse. Then apply Alumiprep, rinse, dry, followed by a 5-10 minute
immersion in Alodine for each component. The rest of the day is your
own! Once the Alodine is dry and firm, spray with Sterling 1201/1202
Epoxy Primer/Sealer. This is milspec stuff which leaves a thin and very
tough yellow skin on the components - they use it in FA-18s I am told.
Some say you don't have to prime, but the SAAA builders assistance program
in Australia demands treatment to resist corrosion, so why not use the
best! At the end of all this you have every component smoothed, drilled,
deburred, dimpled, Alodined and primed. Finally you are ready to start
riveting it all together.

Skins clecoed
on
|
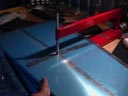
dimpling skin
|
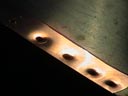
hand dimpler
- ugh
|
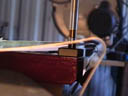
dimpling forward
|

primed
|
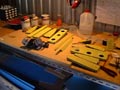
primed
|
5.
Final Assembly
Follow
the instructions carefully here. The very first rivets are the flush
ones that attach the front ribs in the to the skin. Practice first,
as much as you need to make sure you know what to do. I found this difficult
on my own, and had to drill out my first efforts. It helps to have someone
shooting while you buck and always ensure rib and skin are snug together.
Any gaps and the rivet will not set properly. The other side can be
set with flush pop rivets - they looked fine to me. Then you rivet the
skeleton together. With the round-head Universal rivets, push real hard
so the rivet set does not bounce and cause a "smiley". I had
to drill my first three rivets out for this reason. Riveting the skin
to the skeleton was relatively easy. I polished a flat on the side of
the smallest bucking bar from Avery, and I was able to blind rivet with
this bar by myself with good results. In general, I clecoed every third
hole, riveted the rest, and then removed clecoes and final riveted those
holes as well. In the fourth image below you can see the completed rear
spar hanging on the wall. THe final step is to rivet this in place,
but wait until your Technical Consultant has checked all the work inside
first.
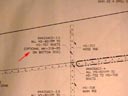
middle rib/skin
|
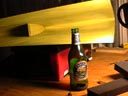
|
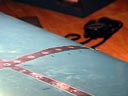
flush pop
rivets
|
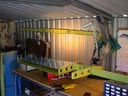
skin-skeleton
|
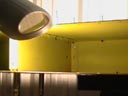
internal pop
rivets
|
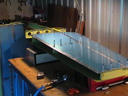
both skins
|
Horizontal
Stabiliser finished Jan 23rd, 2004.